At HEL, our expert staff understand each of your machines, so we can actually fix them— through our machine shop —rather than give you a temporary solution. Our repair process is designed to smoothly identify the problem, replace broken parts, and get the machine working again within your scheduled downtime.
Our machine shop provides incredibly quick turnaround time
In addition to our repair work, HEL operates a large-capacity machine shop designed to facilitate our repairs.
When we say large, we mean it. If your broken piece of machinery or your part is smaller than a pallet, we’re not the right machine shop.
That being said, we don’t mass produce parts. Instead, offering tailored solutions gives us flexibility to provide a fast turnaround for customers—by not having our every hour booked.
Our ability to respond quickly—often within just two days of receiving a RFQ—better serves our customers.
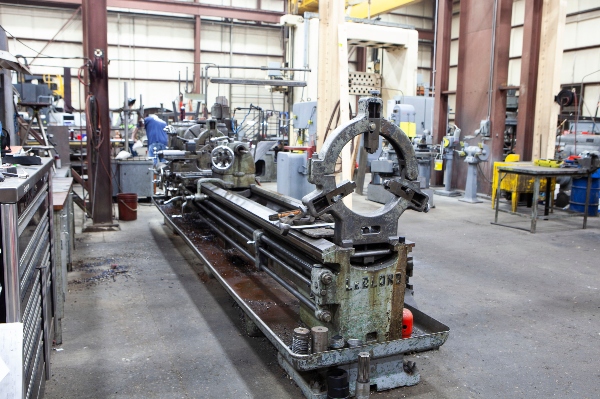
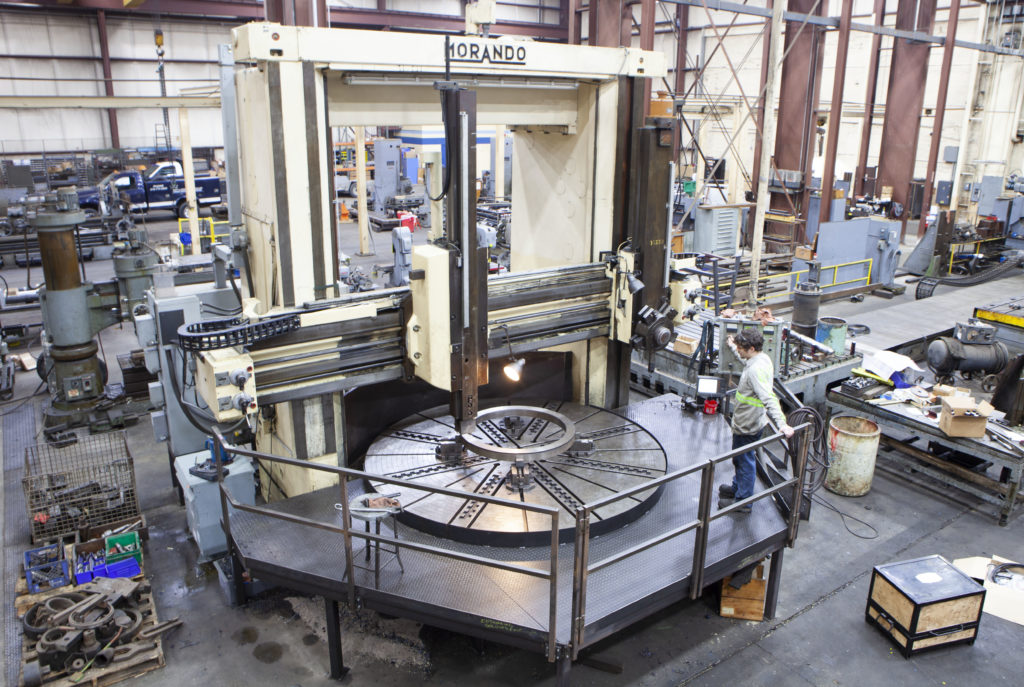
We understand the big picture
We outlined our repair process previously. When ordering parts from the Original Equipment Manufacturer (OEM) is going to require too much downtime for our customers, we use our large-capacity machine shop to create an alternative part.
And, sometimes, the part in question has been discontinued from the OEM, causing a much more troubling situation. When this happens, we utilize reverse engineering techniques to create something that can be used instead.
This is where the benefit of working with a single-source provider, like HEL, comes in handy. We work with you on the full project and understand the big picture of your needs. That’s why we can identify exactly how the part works in conjunction with other pieces it interacts with—preventing premature failure or damage to your equipment.